Prefab homes could soar in value on big four bank move
Building prefabs in a factory can cut construction times down to 10 to 12 weeks - compared to 18-plus months through traditional methods.
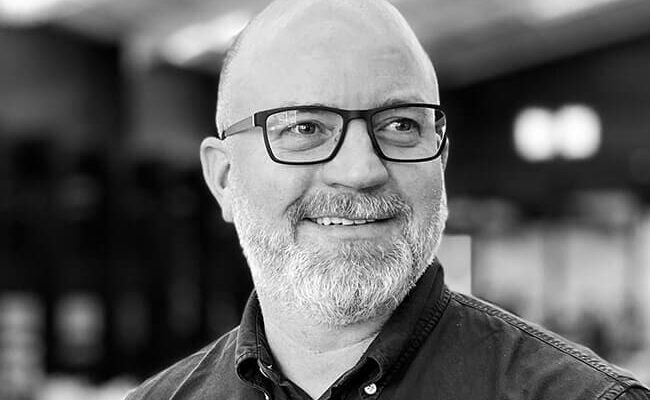
PREFABRICATED homes could see their value soar with banks coming round to offer mortgages.
Commbank announced it was joining prefabAUS, which represents Australia’s off-site construction industry.
The bank – which once shunned prefabs – is also making policy changes to make it easier to buy pre-built housing.
prefabAUS founding director Damien Crough said working with CBA welcomed the move as using prefabricated housing would enhance its role in addressing Australia’s housing shortage.
“With support from CBA, prefabAUS will tackle some of the challenges facing our members and their clients,” he said.
“We are excited to unlock the potential of off-site construction to address one of the nation’s most critical challenges—providing access to high-quality housing at pace.
“Utilising prefabrication, a house constructed in a controlled factory environment is built in 10 to 12 weeks, compared to around 18-plus months through conventional building.”
CBA’s Mike Vacy-Lyle said: “Prefabricated construction is fast, efficient and can play a meaningful role in addressing Australia’s housing shortage.
“To date however, everything about construction has been created with traditional, on-site work in mind, and we need to rapidly reimagine how we support this industry to unlock scale and deliver more quality and sustainable homes to market sooner.
“Overseas in countries like Sweden, 80 per cent of houses are being factory built, and we would expect to see Australia’s prefabricated construction sector expand rapidly.”
Modscape CEO Jan Gyrn welcomed the collaboration between CBA and prefabAUS – and highlighted the impact prefabs could have on the housing crisis.
“We’re able to complete eight modules a day, providing a great option for the rapid delivery of much needed homes for Australians,” he said.
The business he founded in 2006 has now installed a new robotic line at its Essendon Fields facility which is the most advanced of its type in the Southern Hemisphere.
Mr Gryn says it will play a crucial role in delivering large-scale residential projects such as the Affordable Housing Project in Cairns, which is the biggest modular social and affordable housing project in Australia.
More than 1,000 timber prefabs are due to be delivered there.